In the 1990s, Rich Duisberg worked as a consultant in the research and development labs and quality control departments of various car manufacturers around the world. It gave him an interesting, and often amusing, perspective on how cars are made – sometimes badly. This is How not to build a car, Part 2: Bodywork.
The perception of quality, in the world of car interiors, can be defined by two things. The first is quality of materials, those raw ingredients, and the second is reliability of the components and the car as a whole. When manufacturers get these elements right they build a great car, but when they don’t you might end up with something like a Renault Fuego. More on that hot topic to follow.
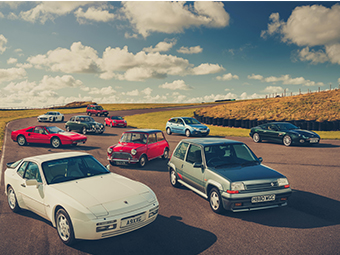
Material choice is important. Touch points are things where there’s a human-machine interface. It could be a physical interface, like the feel of switches, or non-physical, such as the sound of a door closing. Designers spend incredible amounts of time designing and testing these points and material choice plays a big part. We all love the warm feel of leather, but in early days of car manufacture it was considered rather utilitarian to use leather for seating – only the driver, exposed up front in the bad weather would have it for reasons of practicality. Real luxury was wool or velour.
Many luxury cars nowadays have synthetic alternatives to leather. Mercedes-Benz created MB Tex in the ‘60s and it is a robust alternative to the real thing. It is far more resistant to wear and sunlight. BMW uses something called Sensatec for the same reason. Leather in a Rover Sterling, for example, is actually high-grade material, but poor processing meant that many cars delivered to places with sunny climates were rejected as the leather turned a sickly shade of green. That’s how not to build a car, Longbridgers.
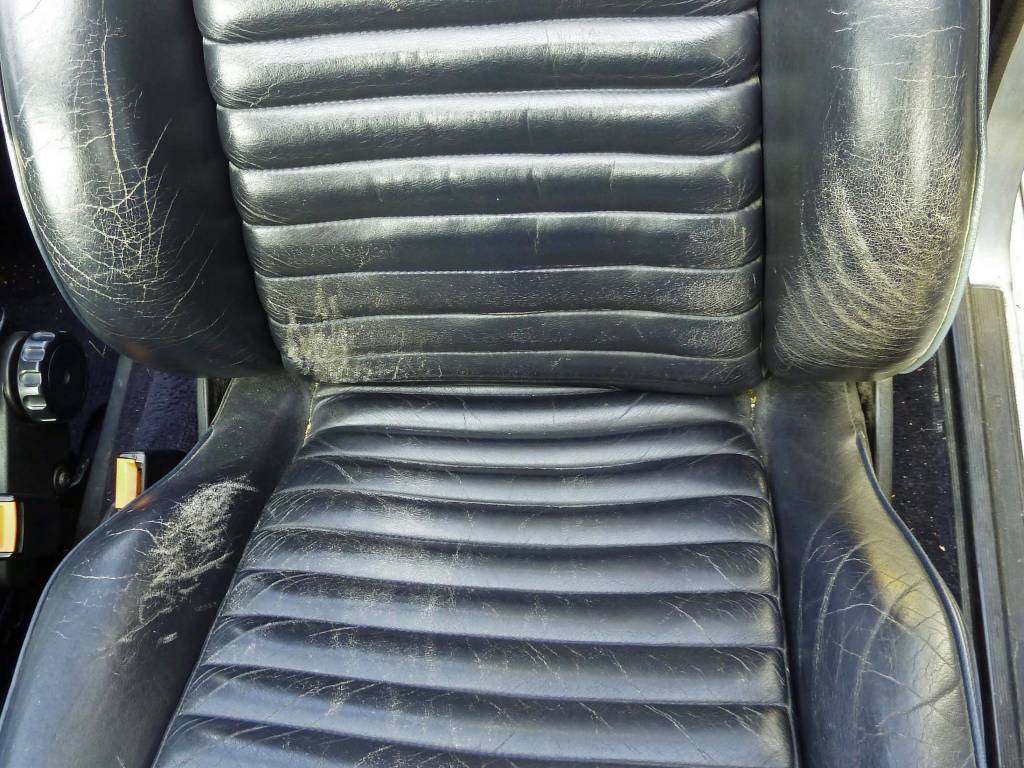
Just as water is a killer of car exteriors (see part one of HNTBAC for stories of rust), sunlight is a killer of car interiors. The UV light that causes skin cancer in humans causes a photochemical effect in the polymer structure of plastics used in cars, degrading them over time. Look at the dash top of some cars, like the Porsche 924. It will eventually crack in the sun. This can expose the foam within, which then soaks up humidity in the air, causing swelling, which bursts open those sun-induced cracks further. An ugly cycle. Understanding of this phenomenon was rather rudimentary when that sort of car was designed.
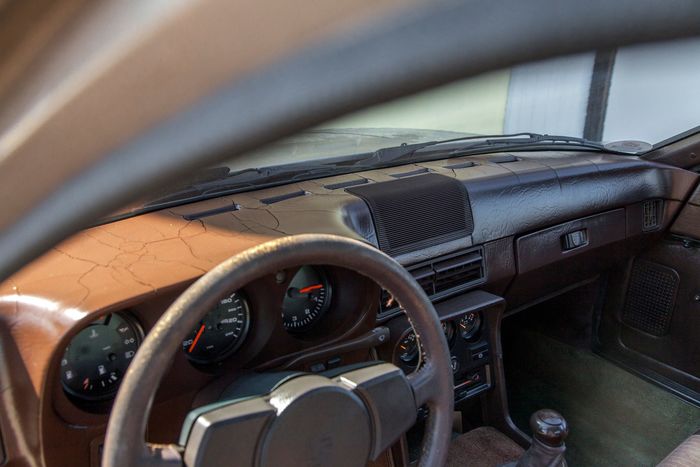
The thermal cycling of heat also affects injection-moulded components. If you imagine squirting hot plastic into a mould to make a complex shape, the plastic forms joins where the fluid meets inside. And there’s a little nipple left where the injection tool has been. As the component heats up and cools down repeatedly, the miniscule difference in material homogeneity means the component doesn’t expand and contract the same way throughout, and it can eventually fail in those join areas. Building a car from plastic bits is quick and cheap for mass production, but not without it’s issues. In case all this is getting a bit geeky, we’ll take a quick look at the Renault Fuego.
I love the Fuego. It sounds exotic, looks exotic, and I thought it was cooler than the Ford Capri and Opel Manta back in the ‘80s. (Disagree? Vent at me in the comments, below.) But this is classic example of where a manufacturer chose poor materials and had poor quality control. The Fuego sold in tens of thousands in its time but poor interiors (and many other things, to be fair) mean that there’s barely a dozen left on UK roads. Many of the interior parts were plastic, shared with the Renault 18 on which it was based, and shortcomings in the electrical design meant that, anecdotally, some even caught fire. Fuego indeed.
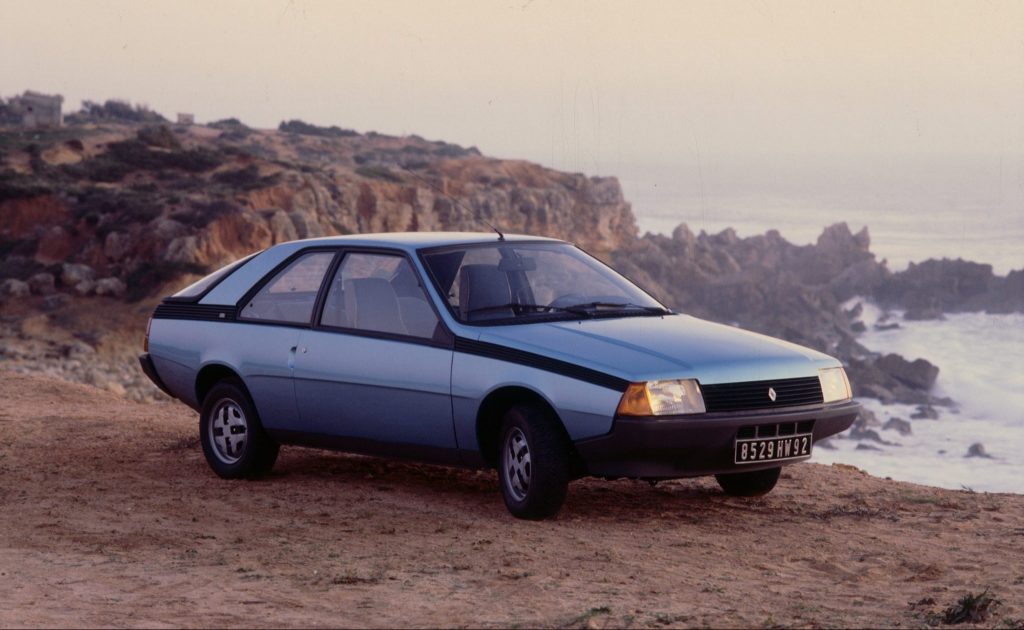
Another unpleasant surprise for Fuego drivers was, reportedly, on occasion the steering wheel might come off in their hands. I do not know the root cause of this but, based on my experiences in the car industry, it comes as no surprise. Some manufacturers mitigate against poor quality by adding in redundancy. Many Ladas came with a starting handle until the ‘90s in some markets, and there are some Volgas with both electric windows and a manual handle – just in case.
Of course you can have the most tactile, robust materials, designed into the most reliable components, but if they’re not assembled properly then you’re not building a car properly. Manufacturers today employ teams of quality controllers who will take up residence in any sub-supplier’s factory that is failing to conform to defined standards until process faults are identified and fixed. However, in the past some seemingly cared more than others. I recall a visit to a tier one supplier – effectively a car company’s most trusted supplier – in Italy, in the ‘90s. When I pointed out a clearly defective wiring loom the quality manager shrugged and said “What?! It’s only for Fiat!”
There are three old Fiats in my household, and I’m a dab hand with the multimeter. Yesterday’s manufacturing shortcomings are my mucky-handed pleasure today.
Finally, consistency and discipline is the way to build a good car – bringing well-designed components together on the production line, perfectly, every single time. The Japanese car manufacturers knew this before their peers.
Production lines in Japan often employ people who happily perform exactly the same task, over and over, for years. There’s a tall story of a Nissan production line worker in the UK, driven half mad by monotony, who sent a production line parts delivery robot down the A19 to rid himself of its constant beeping. I do hope that’s true. But there would be no such rebellion in Japan; Co-founder of Honda, Soichiro Honda, (Takeo Fujisawa was the other founder, in case you’re wondering) was known to visit production lines and maintain discipline in person, once lightly tapping a worker on the head and lecturing, “You damned fool. This is how you’re supposed to tighten bolts!”
Read more
The Parts Bin: Shared Parts for Classic Cars
From wreck to dream drive: Simon Kidston’s astonishing £400,000 restoration of a one-of-a-kind Lamborghini Countach LP400
What a quietly fabulous looking thing the Fuego was. Still futuristic. Thank you for the reminder. But you’re right. I saw more in the scrapyard than on the road.