They’ve been called most things, depending on where people live. Birmingham Screwdriver, Manchester Screwdriver, Yankee Screwdriver, nicknames for the venerable hammer are all wry terms of endearment. The joke being of course, the use of brute force instead of taking the more sophisticated route of using the right tool for the job. But actually, knowing which hammer to use for which job in the workshop, and what each one is capable of reveals them to be anything but crude. In fact, some can even be described as precision tools.
All hammers are used to exert force on an object, using the most basic principles of moving a mass (the hammer head) with a lever (the handle). But enough of the fancy stuff, let’s start with the basic use, shifting or driving things. Using a hammer to drive something in or shift something that is stuck is probably the most common use anyone would think of, but what happens when you do it?
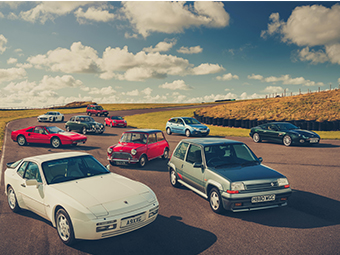
That workshop basic, the engineer’s ball-peen (or ball-pein) hammer is a good example. They have a long handle and a forged steel head with a hammer face on one side and a ball on the other. The ball is literally used for peening, the process where each blow crushes the surface of the job at that point, relieving stress in the metal, typically along a weld.
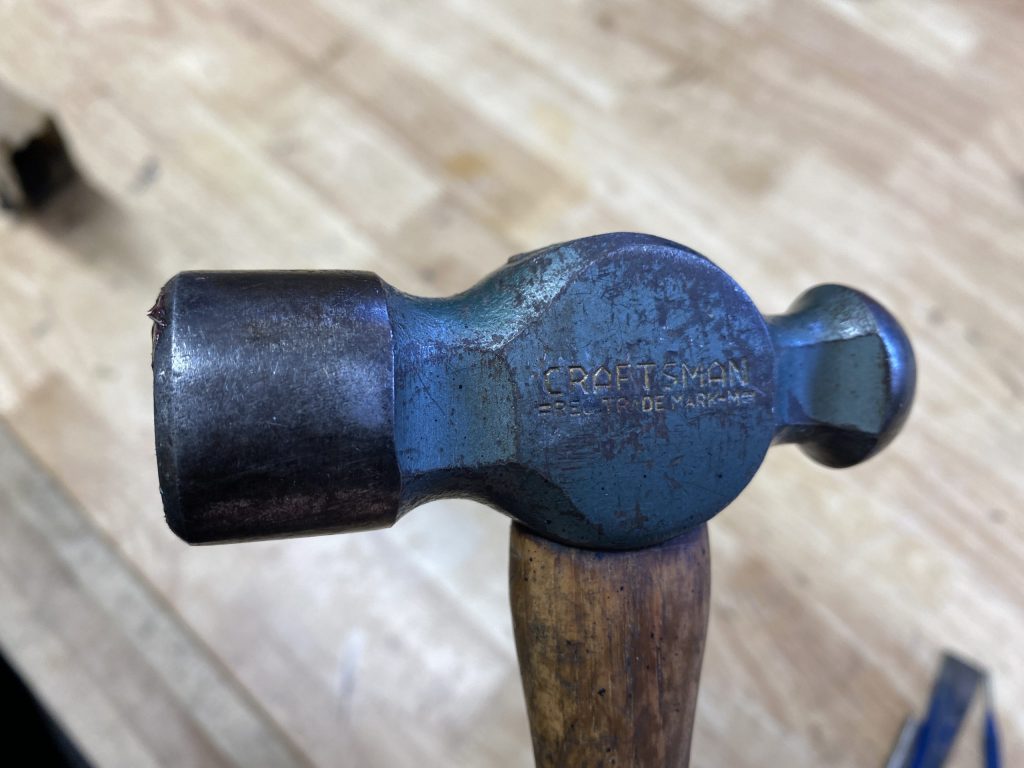
Their most common use though is as a general-purpose engineering hammer. They come in different sizes but a traditional all-rounder is the 2lb engineers ball-peen hammer. These days they do come with composite handles but in my book it’s hard to beat the original oak handle type which is a lovely thing to own and lasts a lifetime.
If something needs a good tap to free it off and the ball-peen is the weapon of choice, the heavy forged steel head falling on target may well do the job, but it may also do a lot of damage. There are plenty of examples of damage left by hammer blows on classic car parts and that’s not the way to go.
The simple fact is, a heavy chunk of steel moving at speed will damage the surface it hits. One way to prevent that is to cushion the surface from the blow with a softer material, like brass. If you’re tapping a bolt out of its hole for example, use too soft a cushion and the energy is absorbed to the extent that nothing happens, but a brass drift will do the trick nicely while maintaining the crisp shock need to shift it, without inflicting damage.

Club hammers with shorter handles and a heavier head (typically 4lb) are useful because they can exert more force at a lower velocity, which can be potentially be less damaging. In some circumstances gently easing a panel with a club hammer and block of wood to spread the load can work well, for example.
Some hammers or mallets are made of softer material to avoid damaging surfaces, the traditional example being a hide or copper mallet, often with a steel casing and a double-sided head made of hide on one side and copper on the other. These are specifically designed for shifting things where weight is needed to provide plenty of inertia even at low speed, but avoids damage. Stuck brake drums are a good example where a hide or copper mallet is ideal.
Other versions are hard nylon mallets, and rubber mallets, both useful for lighter jobs. Dead blow hammers are typically made from soft, rubberised material containing lead shot to add weight. Dead blow means they don’t rebound when they meet the surface and are less likely to cause damage.

Specialised hammers have a role to play in precision work too. Panel-beating hammers sound brutal but for working and repairing panelwork a set of these is a must. Sets include a variety of different types of hammer with different shaped heads and dollies which are hardened steel, shaped blocks that are held behind the sheet metal being worked.
Panel-beating hammers and dollies have polished surfaces to avoid leaving blemish marks and should be reserved only for sheet metal work (more on panel-beating in a future column). Even more specialised are bossing mallets, with hard wooden teardrop-shaped heads used in conjunction with a leather sandbag to form concave shapes in sheet metal.
So that gives an overview of some of the various types of hammer designed for different uses in the workshop and something to think about for anyone starting out. It should go without saying that using hammers involves common sense for both safety and avoiding damage, and giving credence to those old nicknames by taking one to an engine’s most delicate parts is definitely a no-no!
Read more
6 essential hand tools for every DIY toolbox
Socket Set: Choosing spanners for DIY
8 tools to up your DIY game
Hammer handles/shafts are Hickory, not usually oak. Inertia is the tenancy to stay in position, kinetic energy is that imposed by your swinging hammer to impose movement.
As the first comment reports, hammer handles are NEVER oak, it is too brittle. In the USA hickory is the preferred wood, but here in the UK it is usually ash, which has a resilient quality. The same wood as used in the framing of traditional coach built car bodies.
Not really a very well informed piece, I echo the comments above about the types of wood used for handles, Ash or Hickory – never oak.
No mention of Cross Pien, Claw, Tack, Upholstery hammers, the list goes on.
Also no mention of the excellent hammers still made in Birmingham by Thor.
while working in a BMC garage we always called the hammer a 18G1