Plenty of parts have an effect on the handling and ride characteristics of a car, but the damper is critical in a properly functioning suspension. We all know the basic premise: A piston moves in a pressurised cylinder to help control compression and rebound. But do you really know what’s inside or how it’s built? Let’s take a look inside the Bilstein factory in Germany and find out.
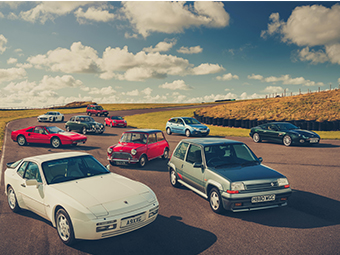
The plant employs 180 workers and manufactures a whole range of products that start as raw materials before they are sorted and distributed within the building to various stations for processing. The facility is large enough to handle the entire process of turning raw materials into finished pieces, but too small to store many finished parts. That means delivery and pickup operations happen five times a day to keep everything running smoothly.
The assembly line is broken into three parts – pre-assembly, main assembly, and final – before finished parts head out the door to the warehouse. The pre-assembly area is where a lot of the dirty work gets done, including welding and machining to build sub-assemblies that will be fit together as they move through the process. Before that can happen, some testing is required, though; a special machine tests the freshly welded damper tubes by filling them with helium. A green light tells the technician that the part can move forward, but if the part fails the test by leaking, the testing machine itself removes the piece to eliminate the chance that a bad part might end up in assembly.
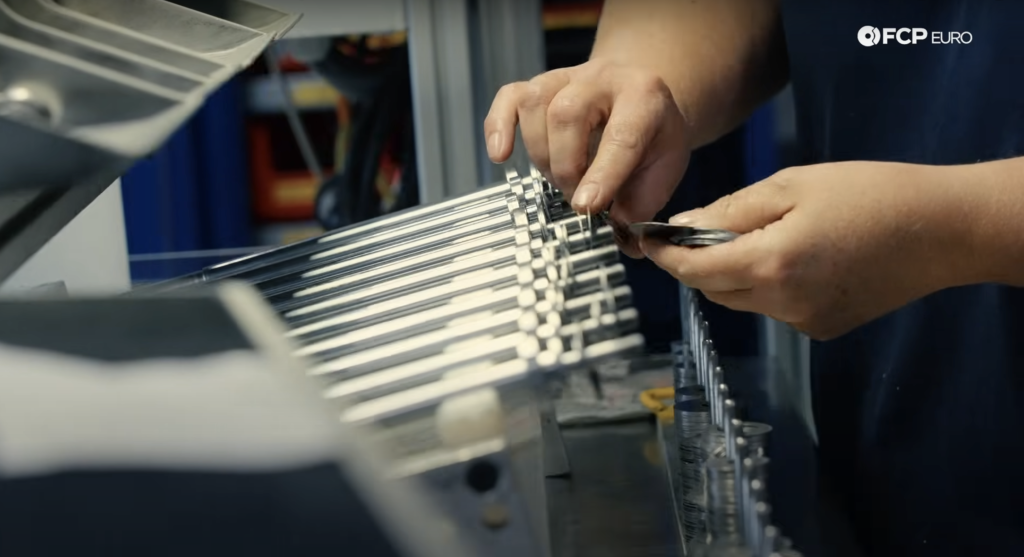
There is no shortage of high-tech equipment to handle a lot of the plant’s operations, but there’s plenty of human presence, too. Bilstein staff visually inspect pieces between steps and ensure the product is as expected. Human hands also tackle the delicate work of assembling the shim stack, or the small, precision, washer-like pieces that set the characteristics of the damper and how it flows fluid during use. Each type of damper has its own “recipe” for the shim stack, and that means it is easier for a person to assemble as they can adapt to changes more quickly than a machine.
The final step is applying the recognisable yellow paint. The paint line is comprised of seven different steps that vary from washing off any oil residue from the filling just one step prior, to drying and ensuring the paint is fully cured before the final touches.
This detailed process highlights just how complex many of the pieces of our cars can be. Getting the massive assembly of parts we call vehicles to operate properly is an intricate business, and nothing illustrates that as much as looking at the effort that goes into making just one part of the thousands required.